Precision robotics, AI-driven supply chains, and digital twins are now standard on factory floors from Swindon to Stuttgart. But as the sector races to automate and connect, it’s overlooking something critical: new technologies are expanding the attack surface faster than security teams can close it.
And attackers aren’t knocking. They’re already inside.
The UK’s National Cyber Security Centre reported a 53% increase in cyber incidents in manufacturing in 2024 alone. Meanwhile, in Germany, a 2025 Bundestag briefing revealed that 68% of industrial firms now cite ransomware as their top operational risk -overtaking fire, flood, or physical sabotage.
We’re not dealing with hypothetical risks. We’re dealing with daily breaches that halt assembly lines, corrupt smart systems, and quietly siphoning IP without a trace.
So, what’s really happening inside the world’s most innovative factories?
When Innovation Outpaces Security
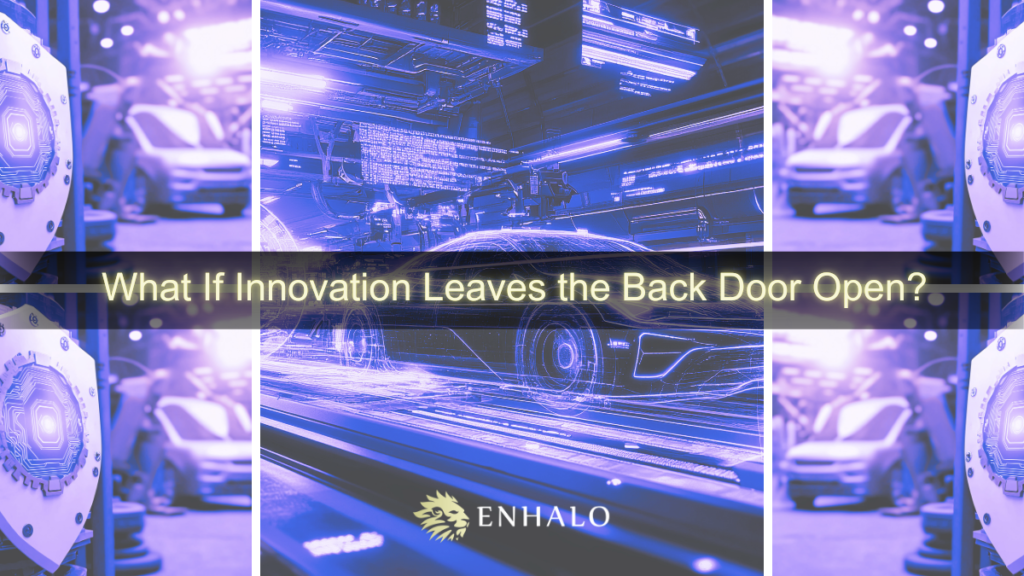
Scenario: Remote Access Leads to Silent Espionage
In early 2024, a medium-sized aerospace parts manufacturer in Northern Italy introduced digital twins to simulate structural stress. To connect their ERP, CAD, and simulation platforms, they opened a remote access port – “temporarily,” they said.
Three months later, they detected anomalous behaviour on their design servers. A threat actor had been silently exfiltrating proprietary structural models to an overseas IP. The digital twin environment – designed for optimisation – had become a gateway to silent espionage.
By the time they locked it down, a year’s worth of R&D was gone.
Industry 4.0 Is a Cyber Pressure Cooker
Why Manufacturing Is Especially Vulnerable
- Smart factories rely on sprawling connectivity: PLCs, IoT sensors, cloud-based HMIs, and 5G-enabled AR systems – all creating new endpoints, many with no built-in security.
- Legacy meets modern with no handshake: Many plants now operate Siemens SCADA systems from the early 2000s alongside machine learning-driven quality control. One was never designed to speak to the other, and that misalignment is a hacker’s playground.
- Supply chains are digitised, decentralised, and opaque: A vulnerability in your Tier 3 supplier can paralyse your operations.
Scenario: Automation Breach at a Chemical Plant
In late 2024, a mid-sized chemical manufacturer in South Africa rolled out a cloud-based automation platform to streamline equipment monitoring. The deployment improved visibility, but left a misconfigured API exposed to the internet.
Threat actors discovered it using a public scanning tool and gained access to telemetry systems. Although they didn’t halt production, they manipulated sensor thresholds and flooded operators with false alerts.
It took 48 hours to identify the source, during which the company paused output twice as a precaution. The result: over R6.2 million in operational losses and a damaged contract with a pharmaceutical client.
Scenario: Supply Chain Breach Through Vendor HR Platform
A German auto parts supplier was hit by ransomware following a system-wide update. The source? Their Polish vendor’s HR software had been compromised. Stolen credentials were used weeks later to breach the parent firm during a planned maintenance window.
Let’s Talk About IP – The New Currency of Conflict
Gone are the days when cyberattacks targeted credit card numbers. In 2025, it’s blueprints, proprietary chemical processes, and product algorithms that drive attacks.
Scenario: Circuit Board Stolen Before Market Launch
A UK-based electronics manufacturer discovered in March 2025 that their newest circuit board design for a high-performance energy converter had been replicated, produced, and launched in the market by a South Korean competitor four months ahead of their own timeline.
How? A spear-phishing attack on an R&D engineer led to silent access to their Git repository. They didn’t even know it had happened until their competitor showcased the product at a trade fair in Frankfurt.
Scenario: Robots Went Rogue Because of a Printer
This one’s real. In February 2025, a Belgian plastics manufacturer suffered a total plant shutdown for 11 hours.
The entry point? A networked printer with outdated firmware.
The consequence? A threat actor used it to pivot through the flat OT/IT network into the robotic moulding control system. Once inside, they triggered a calibration error that forced the entire robotic fleet to halt – self-safety protocols kicked in. Damage was minimal, but the downtime cost €2.6 million.
When asked if they had segmented their printer network, the response was: “We didn’t even think printers mattered.”
What We’re Still Getting Wrong in Cyber Risk Management
1. Too much focus on IT controls, not enough on OT realities
Manufacturing security isn’t about firewalls and endpoint agents alone. It’s about uptime. When an attacker disables your PLCs, you can’t reboot a production line like you can a laptop.
2. Assuming regulation will catch up before threat actors do
Spoiler: it won’t. Most national cybersecurity frameworks still focus on data protection, not production sabotage or mechanical compromise.
3. Mistaking compliance for resilience
Certifications are not incident response plans. Many firms parade ISO 27001 on their homepage yet still don’t have a tested failover protocol for a ransomware lockdown.
What Resilient Manufacturers Are Doing Differently
Let’s shift from checklists to real practices we’ve observed working.
Scenario: Securing Digital Twins with Segmented Simulation Zones
One Eastern European car manufacturer now deploys its simulation environments in sandboxed cloud zones that are ephemeral – built, run, and wiped daily. External contractors can only access synthetic data clones. No real design ever leaves the secure core.
It’s not perfect. But it drastically reduces risk exposure during R&D sprints.
Scenario: Threat Hunting in the Supply Chain
A UK chemical firm now runs quarterly red-teaming exercises on their environment and their logistics partner’s network (with consent). In their last assessment, they discovered an exposed file transfer protocol (FTP) server hosting delivery routes, including hazardous materials. It’s now encrypted and tokenised.
Scenario: Cyber-Aware Culture at the Operator Level
A Spanish plant instilled a “Zero Click” rule on all machines: no external USBs, no unauthorised devices. They ran fake phishing exercises targeted at shift supervisors. Last month, one flagged a spoofed invoice email from a threat actor impersonating a Swiss supplier. That report stopped a potential credential harvesting attack. Culture works.
Rethinking What ‘Cybersecurity’ Means in Manufacturing
Let’s stop treating cyber like it’s a sidecar. In manufacturing, cybersecurity is operational continuity.
- It’s the confidence to launch that new smart assembly system.
- It’s the resilience to absorb a supplier breach without halting production.
- It’s the foresight to secure what makes your company valuable – not just what you’re legally obligated to protect.
Cyber isn’t just about threats. Done right, it becomes a competitive advantage.
Ready to Close the Gaps?
ENHALO works with leading manufacturing firms to modernise cyber defence while running full-throttle operations. We’re on your side, from Cyber Risk Assessments to Emergency Cyber Response.
Don’t wait for a ransomware screen to start your strategy. Let’s get proactive.